What is Cement Hydration?
Without adding water in concrete cement cannot bond to aggregates. It gains its cementing properties when we add water to the dry cement mixture. After adding water to cement, a chemical reaction happens between cement and water, this reaction is called hydration of cement.
Stages of Cement Hydration Process
With the mixing of water, hydraulic cement compounds react with each other and make hydrated compounds with very low solubility. The cement hydration process is not instantaneous.
The reaction is faster in the early stages and continues indefinitely at a reduced rate. Unless the cement is very finely ground and reground with excess water to regularly expose a fresh surface, it cannot be fully hydrated in a year or more. We can divide the process of hydration of cement into 5 phases,
- initial mixing reaction
- Dormancy
- Strength acceleration
- Speed Reduction
- Steady development
1. Initial Mixing Reaction
Initially, after mixing the water and cement, there will be a temperature peak. Aluminate (C3A) reacts with water (H2O) to make aluminate hydrate. The energy which is released in these reactions can be the cause of the initial peak.
2. Dormancy
The result of stage 1 is the surface coating of cement particles. This kind of coating can not only increase the dosage but also slow down the hydration speed because the ability to obtain water is not as good as when mixing concrete. The hydrated concrete remains stable, while the concrete surface remains fluid.
At this stage, concrete remains in liquid form and it is used to transport and pored. The length of this stage depends on the mixing amount of each concrete, so it can be optimized according to winter pouring, transportation time, and other applications.
This stage ends with the initial setting of concrete.
3. Strength acceleration
Since the reaction between calcium trisilicate and calcium disilicate (C3S and C2S) generates heat, silicate hydrate CSH is generated (the increase in heat is also due to other secondary reactions). At this stage, the production of CSH also has a significant effect on the strength of concrete.
In the application of large-volume concrete, it is very important to monitor the changes in internal temperature, because the temperature of the concrete will rise rapidly at this stage, reaching the internal temperature, such as 70-80°C (in some cases even higher). It is generally not recommended that the temperature exceed 70°C.
4. Speed Reduction
At this stage of cement hydration, the temperature reaches its maximum level, and free particles are now reduced, thus slowing the rate of temperature rise.
This stage usually complete with the required strength, and the concrete formwork can be removed now. Monitor the maturity and temperature of the concrete, thus enabling the user to get an accurate time when possible
5. Steady development
This is the final stage of the cement hydration process, Now, the hydration of the cement process has slowed down and continues to slowly complete the remaining usable water and cement particles. The formwork is now usually removed, and over time (which may take a long time), the concrete will complete the process of hydration of cement and reach its final strength.
Read Also: Properties of Cement! Properties of Cement that effect Quality
Mechanism of hydration of cement
The hydration of cement can be categorized into two different ways. The first is the “through solution” mechanism. In this case, the cement compound dissolves to produce a supersaturated solution from which different hydration products are precipitated.
The second is that water erodes the cement compound in a solid state, causing the compound to gradually enter the compound through the surface over time. During the reaction between cement and water, two mechanisms, “through solution” and “solid-state” may occur simultaneously.
Heat of Hydration
The reaction of cement and water is exothermic. This reaction releases a lot of heat. This release of heat is called the heat of hydration.
This can be clearly seen if you put freshly mixed cement into a vacuum flask and read the mass temperature intermittently. The heat of hydration has become important in the construction of concrete dams and other mass concrete structures.
It has been observed that the temperature inside the mass concrete is 50°C higher than the original temperature of the concrete quality when placed, and it has been found that the high temperature can last for a long time.
Otherwise, the obtained product shows that the unattended tricalcium silicate core is surrounded by a layer of relatively impermeable hydrated silicate, slowing further erosion.
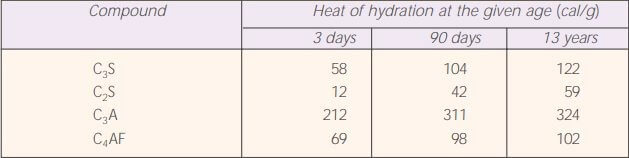
After 28 days of curing, the cement particles can be hydrated to a depth of the only 4µ. Under normal conditions, only particles of cement under 50 μm can be fully hydrated. Ordinary cement usually produces 89-90 cal/g in 7 days and 90-100 cal/g in 28 days.
Cement Hydration products
During the cement hydration process, several products are formed. These products are important because they have bonding or bonding value. The quality, quantity, continuity, stability, and formation rate of the hydrated product are important. Products of the cement hydration process are discussed below.
Calcium Silicate Hydrates Products
During the reaction of C3S and C2S with water, calcium silicate hydrates (denoted as C-S-H and calcium hydroxide), Ca(OH) 2 are formed. Hydrated calcium silicate is the most important product in cement hydration.
It accounts for 50-60% of the solids in the fully hydrated cement slurry. The fact that the term C-S-H is hyphenated means that C-S-H is not a well-defined compound. The morphology of C-S-H showed poor crystalline fiber clusters.
It is suspected that the cement hydration products of C3S and C2S lead to the development of the same hydrated compound. But it was later discovered that eventually, the hydrates of C3S and C2S will become the same.
However, the simple equation given above does not bring the complexity of the actual reaction.
It can be seen that compared with the water formed during the hydration of the cement process, the amount of calcium silicate hydrate produced by C3S is relatively small, while the amount of Ca(OH)2 is relatively large. Ca(OH)2 is not an ideal product in concrete.
It is soluble in water and leached out, making concrete porous, especially in hydraulic structures. Under such conditions, it is useful to use cement with a higher percentage of C2S content.
C3S easily reacts with water and generates more heat of hydration. It is responsible for the early strength of concrete. Cement with higher C3S content is more suitable for cold weather. The mass and density of hydrated calcium silicate formed by C3S are slightly inferior to those formed by C2S. The early strength of concrete is attributed to C3S.
The hydration of C2S is quite slow. It is responsible for the later strength of concrete. It generates less heat of hydration. The calcium silicate hydrate formed is quite dense and its specific surface area is higher. Generally, the quality of the C2S hydration reaction is better than the quality produced by the C3S hydration reaction.
Calcium Hydroxide Products
The other product of C3S and C2S hydration is calcium hydroxide. Compared with C-S-H, calcium hydroxide is a compound with a unique hexagonal prism shape. It accounts for 20% to 25% of the volume of solids in the hydrated paste. Due to the presence of calcium hydroxide, concrete lacks durability. Calcium hydroxide also reacts with sulfates in the soil or water to form calcium sulfate, which further reacts with C3A and causes the deterioration of concrete. This is called sulfate attack.
Reducing the content of Ca(OH) 2 in concrete and overcoming its adverse effects by converting it into cement products is an advancement in concrete technology.
The use of mixed materials (such as fly ash, silica fume, and other pozzolanic materials) is a step to overcome the adverse effects of Ca(OH) 2 in concrete. The only advantage is that Ca(OH)2, which is alkaline in nature, maintains a pH of about 13 in the concrete, thereby resisting the corrosion of steel.
Calcium Aluminate Hydrate Products
The hydration of aluminate has become the subject of many studies, but there are still uncertainties in some reported products. Due to the hydration of C3A, the calcium aluminate system CaO-Al2O3-H2O is formed. The cubic compound C3AH6 may be the only stable compound formed and remains stable at a temperature of about 225°C.
Pure C3A reacts very quickly with water, which may cause flicker. To prevent this flash, gypsum should be added when grinding cement clinker. The amount of gypsum added is related to the amount of C 3 A present.
The hydrated aluminate does not contribute to the strength of concrete. On the other hand, their presence is detrimental to the durability of concrete, especially where concrete is easily attacked by sulfates. Since it hydrates very quickly, it may contribute to early strength.
The requirement of water for hydration of cement
It has been proved earlier that the weight of water required by C3S accounts for 24% of the weight of cement, while the weight of water required by C2S accounts for 21% of cement. It has also been estimated that the chemical reaction with the Portland cement compound requires on average 23% of the cement weight of water.
23% of the water is chemically combined with cement, so it is called bound water. A certain amount of water is sucked into the gel pores. This water is called gel water.
It can be said that bound water and gel water are complementary. If the amount of water is not enough to fill the gel pores, the formation of the gel itself will stop, and if the formation of the gel stops, there is no problem with the gel pores. It is further estimated that about 15% by weight of cement is required to fill the gel pores.
Therefore, to complete all the chemical reactions and occupy the space in the gel pores, a total of 38% of cement water is required. If only water equal to 38% of the weight of the cement is used, it can be noted that the resulting slurry will be completely hydrated, and no excess water can be used to form poor pores.
On the other hand, if more than 38% of water is used, then the excess water will cause bad pores. Therefore, if the amount of water used exceeds the minimum requirement (38%), there will be more excess pores. In all of this, it is assumed that hydration takes place in a sealed container in which no moisture will enter and exit the slurry.
As the hydration progresses, as the volume of anhydrous cement increases, the hydration products also increase. Due to complete hydration, the increase in gel volume may fill the space occupied by water earlier, with a w/c ratio of about 0.6.
If the w/c ratio is greater than 0.7, the volume increase of the hydration product will never be enough to fill the void created by water. This concrete will always remain porous. This means that once the gel is mixed with water, it will take up more and more space.